General customers use gypsum line mold silicone for making silicone molds, and they use more condensed mold silicone. A few customers prefer to use additive mold silicone. The gypsum line mold consists of two components: AB silicone, A silicone, and B curing agent. After mixing silicone with curing agent, it can be formed.
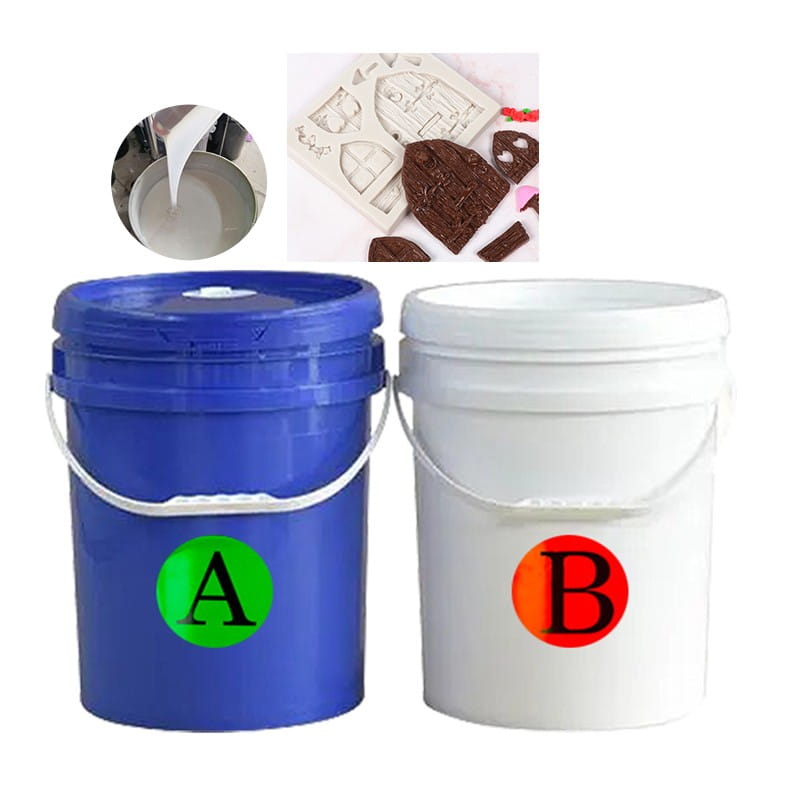
The silicone ratio of the addition mold is 1:1, and the silicone ratio of the condensation mold is 100:2-3. The former is environmentally friendly, while the latter is industrial grade.
Features:
1. Good fluidity, easy operation, and easy demolding;
2. The mold produced does not deform and has advantages such as high temperature resistance, corrosion resistance, acid and alkali resistance;
3. High tear resistance, good tensile strength, reusable mold, and multiple mold turns;
4. Low shrinkage rate (≤ 0.1%), capable of rapid curing at room temperature, and performance can be adjusted according to customer requirements.
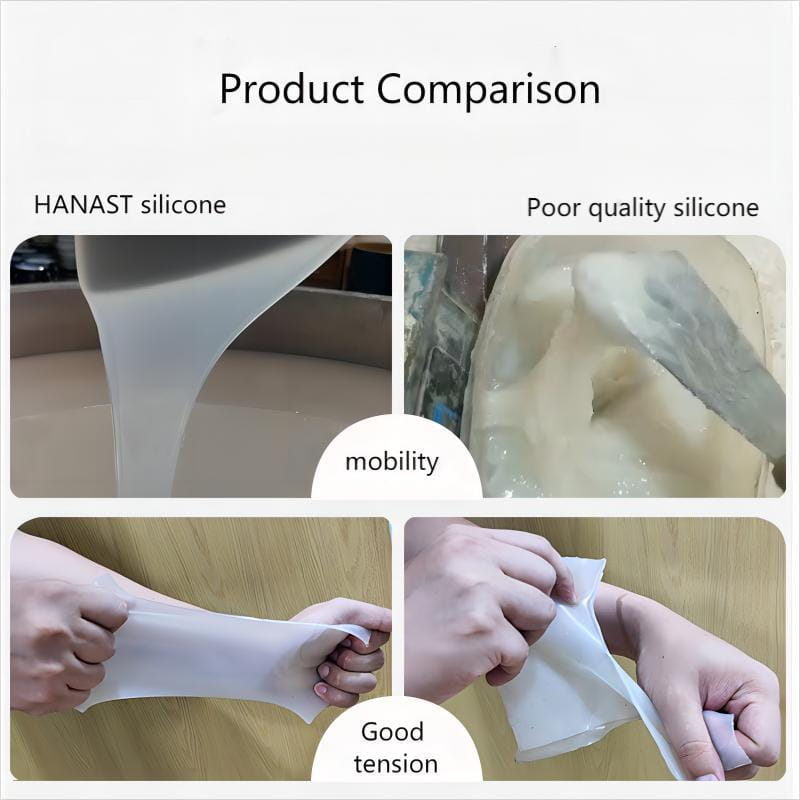
Operation method:
1. Prepare tools: knives, rulers, brushes, scissors, wooden boards, etc;
2. Handle the mold seeds well, fix the mold seeds to the wooden board with oil mud, smooth the oil mud with water by hand, and cut off any excess oil mud around;
3. Weigh and mix silicone according to the structure, pattern, and purpose of the product, with a ratio of 100:2-2.5 between silicone and curing agent;
4. Mix the mixed silicone gel evenly and place it in a vacuum machine to vacuum (vacuum to -0.1mpa, which can prevent bubbles in the mold and affect its quality. If there is no vacuum machine, the addition ratio of curing agent can be reduced, the curing time can be extended, and excess bubbles can be released);
5. Evenly apply the vacuum filled silicone gel onto the mold (usually the second layer can be brushed in about 15 minutes, prepare the required silicone for brushing the second layer, and repeat brushing the first layer 2-3 times);
6. When the silicone does not flow, stick a layer of gauze on the silicone. The advantage of doing so is that it can enhance the strength and tear resistance of the silicone, and then evenly brush a layer of silicone (depending on the size of the product, add an appropriate layer of gauze, usually no more than two layers);
7. After the silicone coating is completed, make a mortise on the edge and fit it with the outer mold to ensure that the mold is not misaligned;
8. After the silicone gel solidifies, the outer mold can be made. Fix the shape of the outer mold with a wooden board, pour the adjusted gypsum into the mold, and apply the gypsum evenly;
9. After the outer mold is fully cured, remove the wooden board, remove the entire outer mold and silicone mold, inspect the silicone mold, trim the silicone mold with scissors, and trim the gypsum outer mold;
After the completion of silicone mold production, it can generally be put into production after 24 hours.
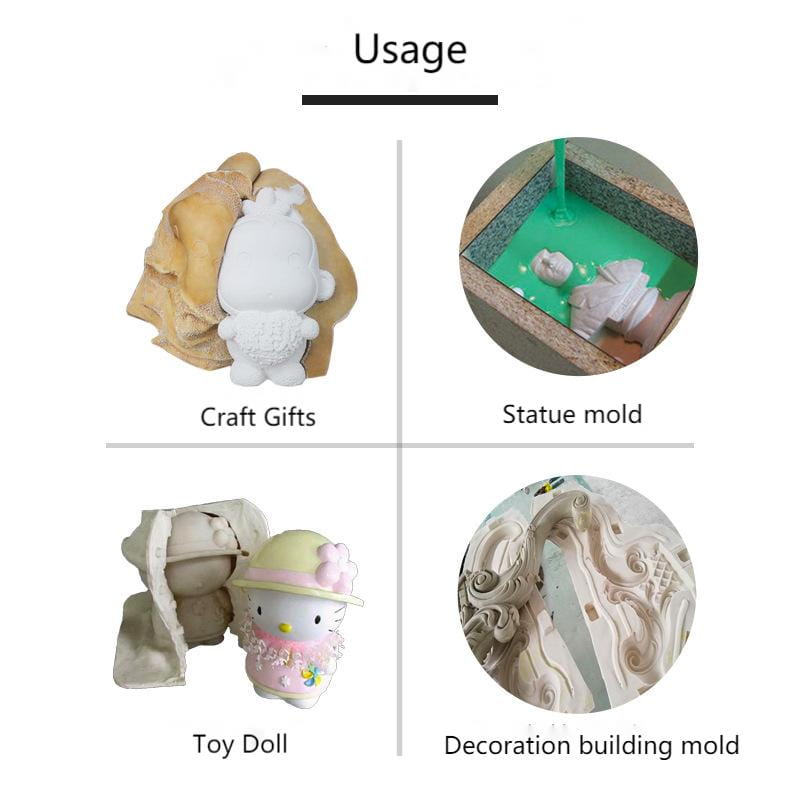
Precautions:
The amount of curing agent added should depend on the temperature, which decreases when the temperature is high. If too much curing agent is added, it will affect the quality of the mold, and the silicone mold will become brittle; Adding less curing agent will prolong the curing time;
2. The time for vacuuming should not be too long. Normally, it should not exceed ten minutes. If the vacuuming time is too long, the silicone gel will solidify immediately, causing cross-linking reactions, making it difficult to apply or pour the silicone gel one by one. This will waste the silicone gel;
In order to ensure the best performance of the silicone mold, it is recommended to put the produced mold into production 24 hours later.
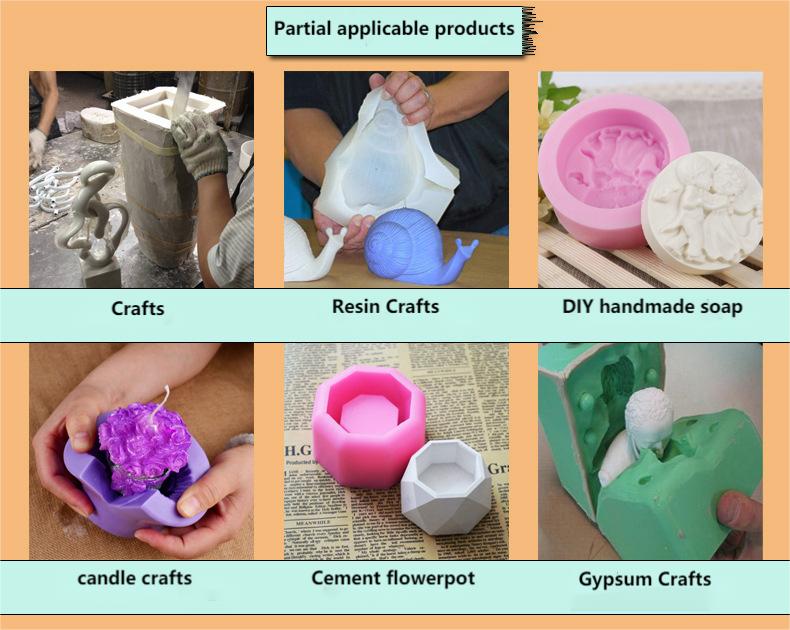
Hardness selection:
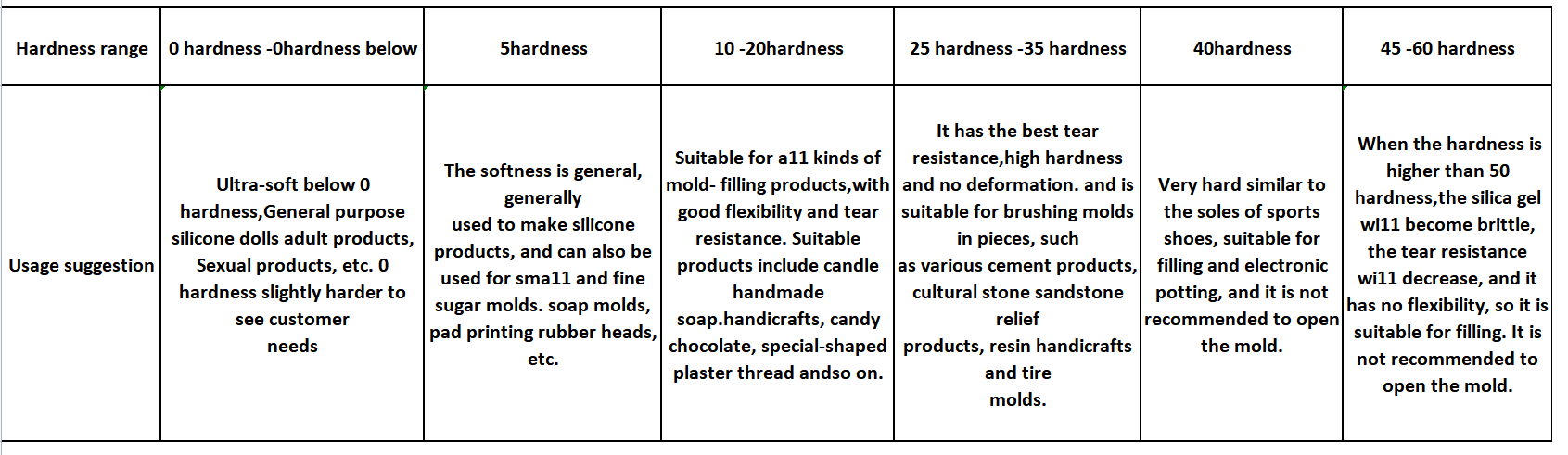
Process parameters:
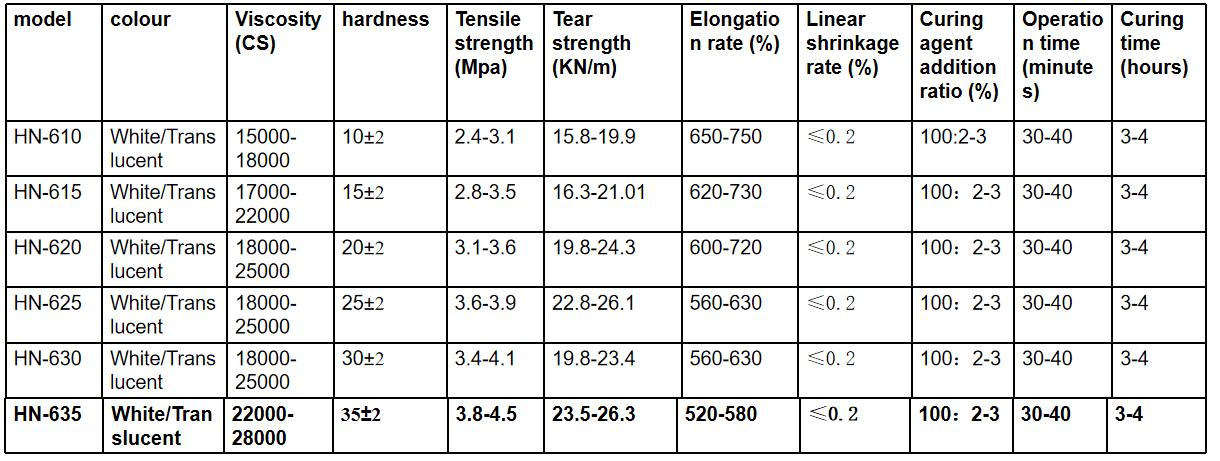
Packaging:
Gypsum line mold silicone is suitable for the replication of various large, medium, and small gypsum crafts, gypsum decorative building materials, and building decoration processes, as well as the production of silicone molds.
Brick carving mold silicone is suitable for the production and product replication of various brick carving molds. It can also be applied to the replication and mold production of various industries such as cultural stones, cement products, sandstone relief, cultural bricks, GRC components, gypsum lines, and so on.
COMPANY PROFILE
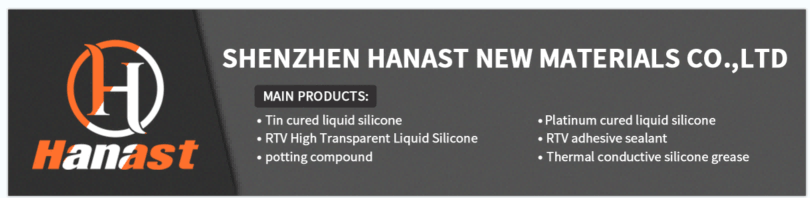
Shenzhen Hanast Technology Co, Ltd. was established on 2019. The factory is located in Sanming City, Fujian Province,
covering an area of 20,000 square meters.
Hanast is a silicone raw material company integrating R&D, production and sales, mainly engaged in conventional silicone
rubber,special silicone rubber, RTV adhesive sealant, two-component electronic potting adhesive, thermally conductive
silicone, thermally conductive silicone grease, lubricating silicone grease, damping silicone grease, platinum vulcanizing
agent and other silicone raw materials.
The products comply with ROHS standard, obtain SGS, Food Grade Certification, and the enterprise passed ISO9001. 2015
certification. Our products have obtained many national invention patents and utility model patents, and are widely used in
silicone kitchenware, high temperature wire and cable, industrial silicone rollers, medical industry, baby products, sporting
goods, adult products, new energy vehicles and other fields.
CERTIFICATIONS
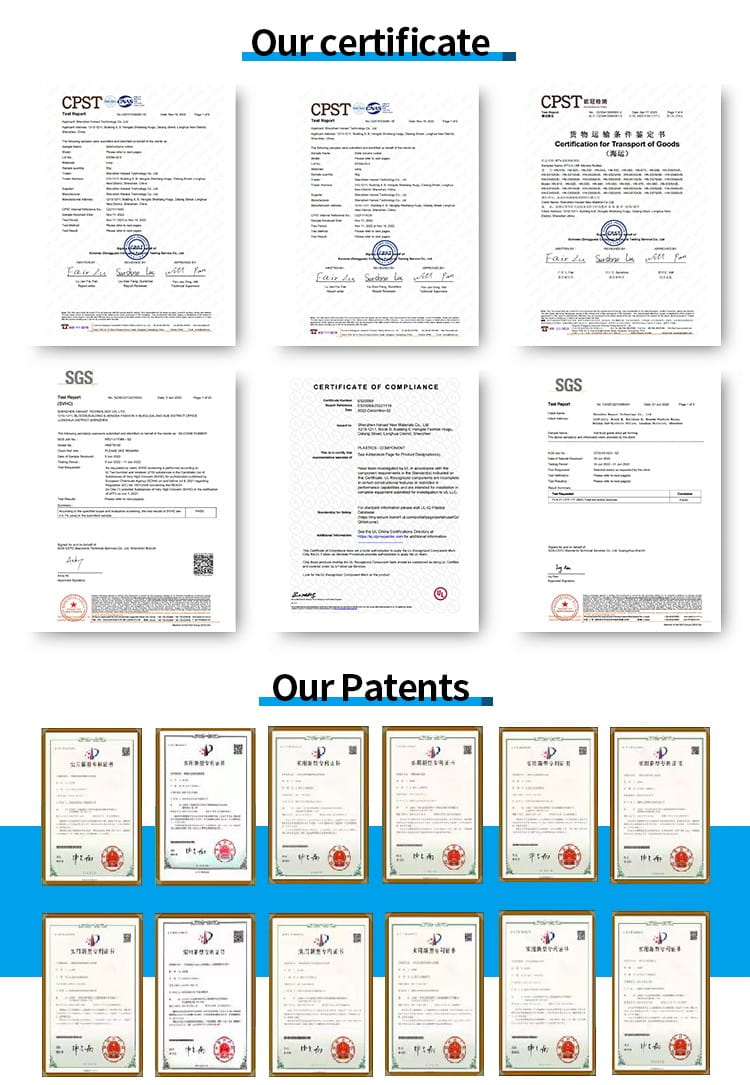
CUSTOMERS